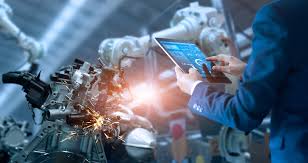
Manufacturing has always been a symbol of human progress—from the first industrial revolution’s steam engines to the rise of assembly lines and computer-aided design. But in 2025, a new force is rewriting the rules of production: robotics. Quietly but powerfully, robotics is transforming how things are made, who makes them, and where they’re produced.
This isn’t just automation. It’s a full-scale reinvention of the factory floor—and it’s changing manufacturing forever.
From Automation to Autonomy
Robotics in manufacturing isn’t new. Robots have been welding, painting, and packaging on factory lines for decades. But the big difference in 2025? Today’s robots aren’t just following programmed paths—they’re learning, adapting, and making decisions on their own.
Thanks to advances in AI, machine vision, and real-time data processing, robots can now:
- Detect product defects on the fly
- Collaborate safely alongside human workers (cobots)
- Reroute themselves in a warehouse to avoid traffic
- Handle custom, small-batch orders with minimal setup time
The result is a leap from automated production to autonomous manufacturing—where machines think and respond to the environment without constant human input.
Smarter, Smaller, and More Flexible
Gone are the days when only mega-factories could afford robotics. In 2025, robotics systems are more affordable, modular, and scalable. Small and mid-sized businesses can now integrate robots into their production lines without tearing down and rebuilding their entire workflow.
Key trends include:
- Collaborative robots (cobots): These lightweight, easily programmable robots work side-by-side with humans, often without safety cages.
- Mobile robots (AMRs): Autonomous Mobile Robots navigate factory floors independently, moving materials between stations or assisting with inventory.
- Plug-and-play robotics: Easy-to-deploy robotic arms and kits are allowing even startups to automate repetitive tasks.
This flexibility is fueling a wave of innovation, empowering companies to adapt faster to market demands and supply chain changes.
Reshoring and Local Manufacturing Comeback
For years, globalization pushed manufacturing offshore to lower-cost regions. But robotics is helping reverse that trend.
With robotic labor doing much of the repetitive and precision work, the cost advantage of overseas manufacturing shrinks. In 2025, many companies are “reshoring” operations—bringing factories closer to home to reduce shipping costs, cut delays, and improve supply chain control.
Local manufacturing, powered by robotics, also means faster customization, lower environmental impact, and tighter quality control. It’s not just efficient—it’s strategic.
Customization at Scale
Traditionally, manufacturing was about mass production—making millions of identical items. But today’s customers want personalization, not just products. Robotics is making that possible.
Modern robots can:
- Adjust quickly to design changes
- Handle a variety of product variants without retooling
- Collaborate with AI to manufacture on-demand, one-of-a-kind items
This means manufacturers can produce customized shoes, smart gadgets, or even medical implants—without sacrificing speed or efficiency.
Safer Workplaces, Smarter Jobs
One of the biggest impacts of robotics in 2025 is worker safety and job transformation. Dangerous, dirty, and physically taxing jobs are increasingly being handled by machines, reducing injuries and fatigue.
But robots aren’t taking away all jobs—they’re changing what those jobs look like.
Workers are shifting from manual labor to roles such as:
- Robot operators
- Maintenance technicians
- Data analysts
- Production planners
- Quality assurance specialists
Companies are investing heavily in reskilling and upskilling programs, preparing the workforce to thrive in human-machine collaboration environments.
Challenges Still Remain
Despite its many benefits, robotic manufacturing isn’t without obstacles:
- Cost: While cheaper than before, advanced robotics still require upfront investment and integration time.
- Skilled labor shortages: There’s a growing need for people who understand robotics, coding, and systems integration.
- Cybersecurity threats: As factories become smarter and more connected, they also become more vulnerable to hacking and digital sabotage.
- Ethical and workforce concerns: Not every worker is easily transitioned to a new role, and the social impact of job displacement must be managed responsibly.
These challenges call for thoughtful policies, inclusive training programs, and ongoing dialogue between industry, government, and labor groups.
What the Future Holds
By 2030, experts predict that robots will handle nearly half of all manufacturing tasks globally. But that doesn’t mean humans are out of the picture. In fact, the factories of the future will be hybrid ecosystems where humans and machines work in sync—each doing what they do best.
Expect to see:
- Fully autonomous “lights-out” factories
- AI-powered supply chains that predict and adjust in real time
- Swarms of small, adaptable robots working together like a digital ant colony
- Global networks of smart factories connected through cloud platforms and IoT
This isn’t science fiction—it’s already underway.
Final Thoughts
Robotics is no longer a luxury for elite manufacturers—it’s a necessity for those who want to stay competitive. In 2025, robotics is delivering speed, safety, customization, and intelligence to every corner of the manufacturing world.